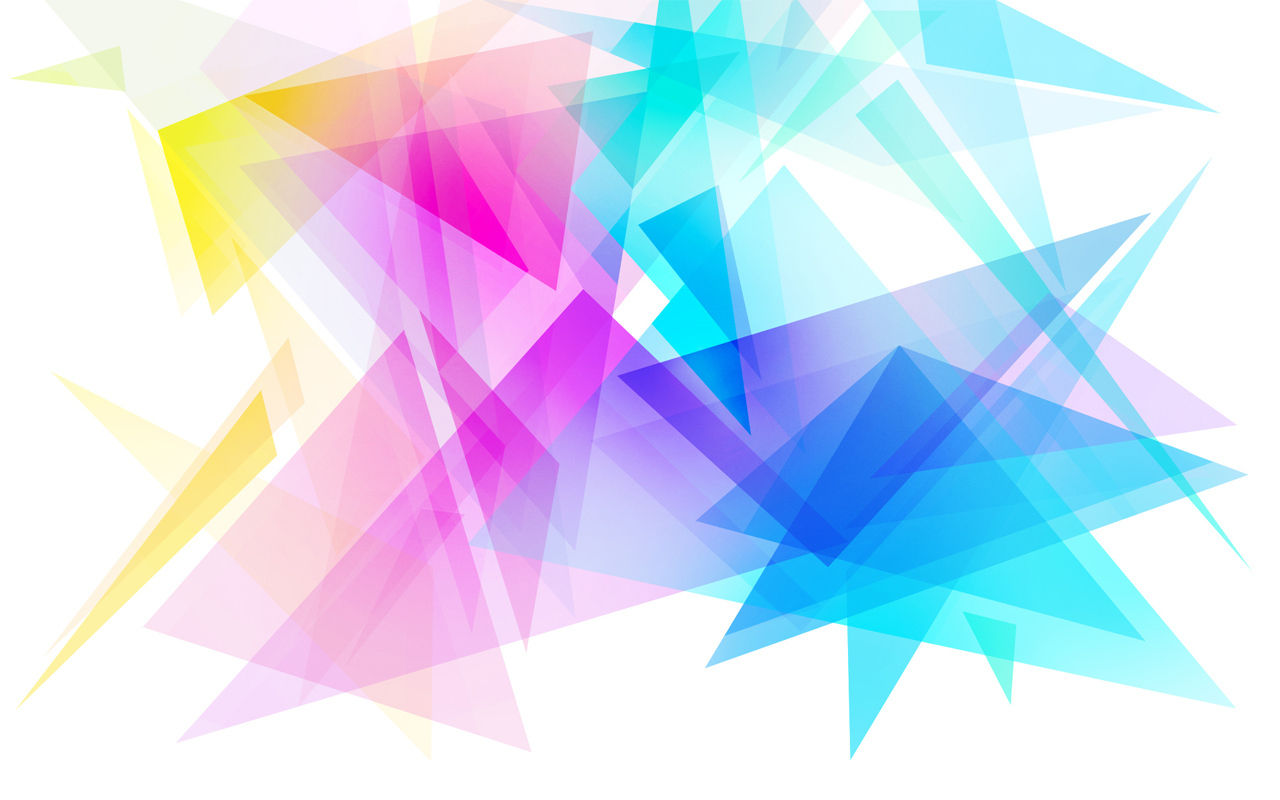
Company Cuts 3D Printing Costs in Half while Solving Environmental Issue
A Chinese hi-tech company with a stick-it-to-the-man attitude is revolutionizing the 3D printing industry by making it less expensive to 3D print. Jiangsu Jinghe Hi-Tech has announcedthe development of a more affordable alternative to traditional PLA and ABS plastic filaments. The company has invented an eco-friendly, straw-based material that can be mixed with plastic to create a 3D printer-ready material that is around half the price of traditional PLA plastic reels.
Solving one of China’s problems
The material, which melts at around 170 degrees Celsius, is made from a combination of dried rice and wheat stalks with plastic additives. Interestingly, its inception arose as a solution to a Chinese environmental issue. Each year in China, excess biomass and leftover crops would be burned by farmers, which led to carbon dioxide pollution and an eventual banning of the procedure by the Chinese government. Jiangsu Jinghe Hi-tech decided to find a way to utilize the significant mass of leftover straw. From here, the material was born.

Not your average 3D printed item
Using the company’s patent-pending technology, the straw is shredded into tiny 2-milimeter pieces and mixed with polypropylene and other additives to create pellets. These pellets can then be extruded to make filament for 3D printers. Unlike the brightly-colored, plasticky looking products usually made with ABS or PLA filament, items made with the straw-based material have the color of natural wood with a plant fiber textured finish. According to Jiangsu Jinghe, producing 14,000 tons of the straw-based plastic can reduce carbon dioxide emissions by 22,400 tons every year.
Not only is the material eco-friendly, but apparently it costs $1600 per ton as opposed to the $3200 you’d shell out for the same amount of PLA. If all goes well and the company begins to manufacture filament for sale, we could potentially see a drastic drop in the price of 3D printing materials. This could be a significant propeller of the industry’s ongoing attempt to break barriers and become a widely adopted technology.